Synopsis: After retiring as a mechanical engineer, Pat Moriarty launched a chair firm and commenced planning a freestanding woodshop on his property. Nevertheless, when he discovered that an outdated industrial constructing in a neighboring city had been transformed into an area for artists, makers, small companies, and startups, he deserted his authentic plan and signed a lease for an area that may accommodate his classic woodworking machines. Not solely did Moriarty get fast entry to an ideal area for his enterprise, however he grew to become a part of a neighborhood of creators, a few of whom he has collaborated with.
After I retired after a profession as a mechanical engineer 9 years in the past, I knew that I wished to spend the remainder of my life doing one thing that was each thrilling and difficult. Having already loved years of woodworking as a pastime, I made a decision it was a pure selection for the subsequent chapter of my life. Inside every week of retiring, I began Conway Chair Firm.
Initially, I meant to construct a freestanding woodworking store on my property. I cleared two acres of land, put in a effectively, and designed a septic system. Nevertheless, someday I occurred to fulfill a glassblower who lives in my Massachusetts city, and after I requested about his store setup he informed me he was shifting into an outdated brick mill constructing one city over in Shelburne Falls. Constructed on the banks of the Deerfield River, the mill had been the house of cutlery producer Lamson & Goodnow since 1837. When the corporate relocated in 2015, the mill’s new proprietor reconceived it as a spot providing inexpensive studio areas for artists, makers, small companies, and startups.
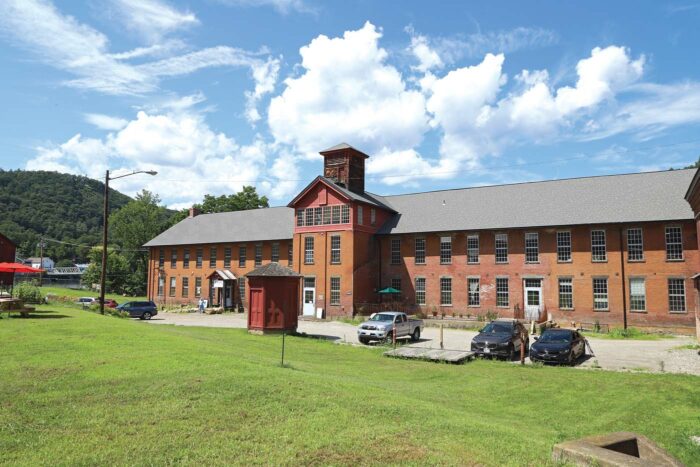
This struck me as a terrific alternative, and the subsequent day I used to be negotiating a cope with the proprietor of The Mill at Shelburne Falls for a 30-ft. by 25-ft. area that includes onerous maple flooring, tall double-hung home windows that line the east and west partitions and fill the area with daylight all through the day, and three-phase 230-volt energy for all of my woodworking machines.
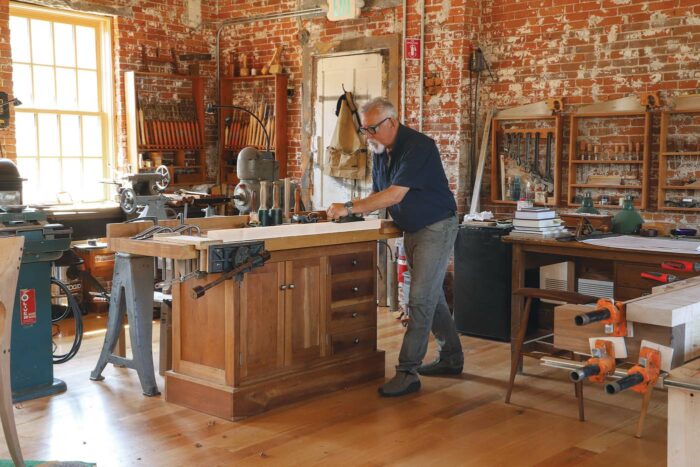
I instantly cherished the area, and over time I’ve found that having a store located in a constructing repurposed particularly for inventive endeavors is a gigantic profit. Being immersed in a neighborhood of artists and makers, every with their very own abilities and dealing on their very own initiatives, results in a contagion of creation. For me, this association has spawned inspiring collaborations with fellow tenants (there are about 40 of us now) and has elevated public visibility of my work by each informal contacts and building-wide open-studio occasions held all year long.
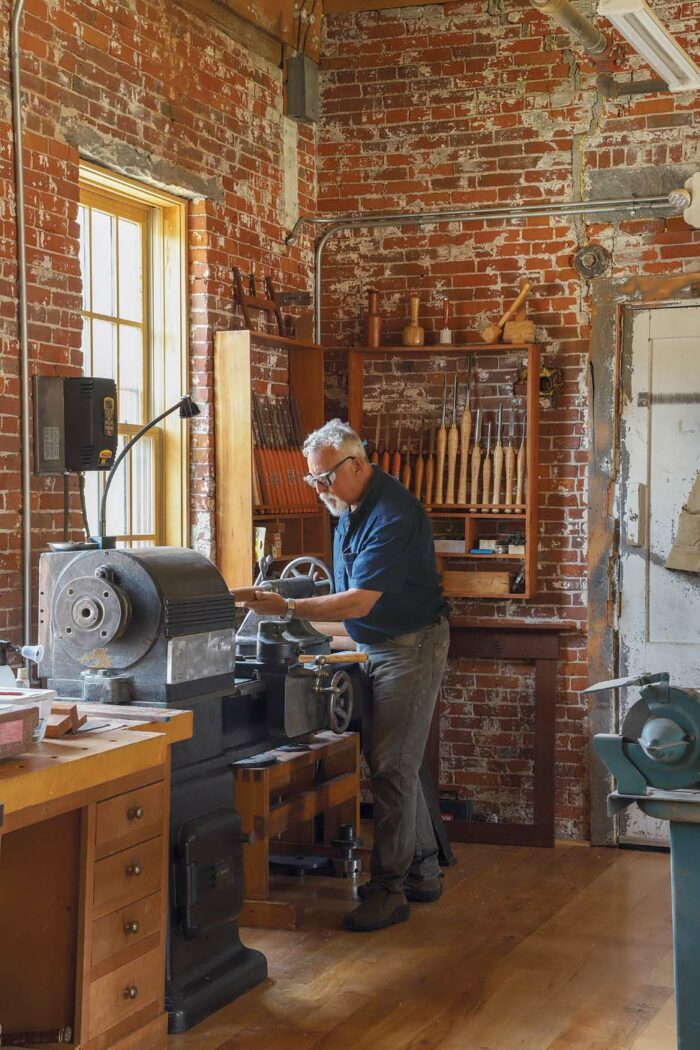
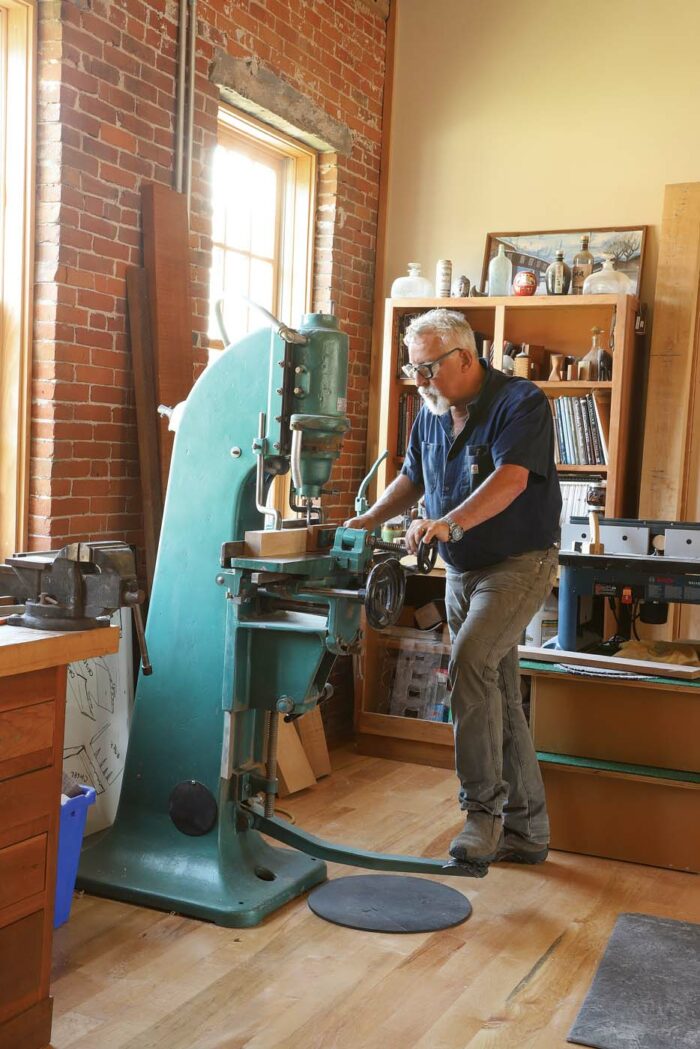
I had been discovering and restoring outdated woodworking machines for a few years, and now all of them have a house. Every classic machine has a narrative. My 36-in. 116 Oliver bandsaw initially resided on the Charlestown Naval Shipyard and was used to assist restore the united statesS. Structure. Then there’s my Northfield 12 HD jointer, with its 3-hp, direct-drive motor and straight three-knife cutterhead. It departed the Minnesota Northfield manufacturing facility on July 2, 1941, to an unknown vacation spot. Sixty years later it was in use at McIntosh & Tuttle Cabinetry Firm in Lewiston, Maine, and in 2005 it was acquired by the New Hampshire–primarily based Littleton Millwork Firm. I bought it from Littleton for virtually scrap worth. After I was restoring this software high to backside, Northfield Equipment Builders—nonetheless in enterprise!—supplied me with elements, labels, and session. This precise machine remains to be made by Northfield as we speak. My store’s oldest machine is an Oliver No. 3 miter trimmer, which was made someday earlier than 1905.
I take advantage of a Fifties Hammond Glider Trim-O-Noticed to chop shoulders on tenons and make crosscuts on four-square inventory. The Hammond Glider was initially used within the printing enterprise to chop lead letter inventory, and its principal function is a cast-iron desk that slides on rails. This function makes it an excellent software to make use of when precise dimensions are vital. Equally helpful is my 1945 Walker-Turner radial drill press, which was initially owned by Pratt & Whitney. This machine’s three-axis drilling capacity fits it completely for chopping compound-angle mortises in chair seats.
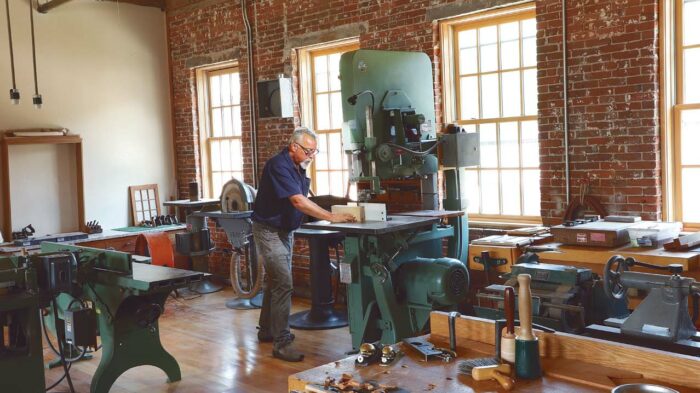
Buying classic woodworking tools requires a great deal of perseverance and due diligence. I by no means purchase tools that has any casting defects (like cracks or beforehand repaired cracks) or is lacking vital parts. I desire to purchase immediately from fellow woodworkers, I by no means purchase sight unseen, and I at all times carry instruments to help within the analysis: dial indicators to verify for arbor run-out, straight edges to verify for desk flatness, an ammeter to verify the motor well being. And the restoration course of might be fairly time-consuming. However the pleasure of utilizing nice outdated machines on this nice outdated constructing makes it effectively well worth the effort.
Sharing a constructing
|
-Pat Moriarty makes chairs in Shelburne Falls, Mass.
From High quality Woodworking #314
To view the whole article, please click on the View PDF button beneath. |
![]() |
High quality Woodworking Advisable Merchandise
Ridgid R4331 Planer
Priced almost $300 lower than the DeWalt 735X, the Ridgid R4331 is a superb worth. Its three-knife cutterhead left splendidly clear surfaces on plainsawn white oak and white pine. It didn’t carry out almost as effectively on curly maple because the 735X.
Rikon 10-3061 10-in. Deluxe Bandsaw
The noticed has two speeds: 3,280 sfpm (floor ft per minute) for wooden and 1,515 sfpm for comfortable metals and a few plastics.
Starrett 12-in. mixture sq.
This correct, strong, well-machined, easy-to-read combo sq. is as nice as ever.
Join eletters as we speak and get the newest methods and how-to from High quality Woodworking, plus particular affords.
Obtain FREE PDF
if you enter your e-mail tackle beneath.