We might obtain a fee whenever you use our affiliate hyperlinks. Nonetheless, this doesn’t influence our suggestions.
By hand or energy? With a spring joint or not?
One of an important joints in woodworking is the sting joint. With out it, our tasks would seem like that they had been constructed from slim popsicle sticks.
The joint bewilders many newbie woodworkers – maybe as a result of there are such a lot of methods to go about it. Which methodology is finest? Which instruments are finest?
The senior workers of Common Woodworking circa 2009 hardly ever agreed on something. And making edge joints was no exception. They did, nevertheless, agree on one precept in relation to edge joints: You aren’t going to get constant outcomes by making your edge joints with a desk noticed blade.
Let’s journey again in time and see how these editors used different instruments and machines to create edge joints that resulted in seamless seams and most glue adhesion.
First: Understanding Historical past
This joint has all the time made woodworkers edgy (sorry). Early written accounts of creating edge joints would tout a wide range of approaches as one of the best to make sure the completed panel stayed collectively.
Some accounts really helpful unfastened splines. Some really helpful utilizing a tongue-and-groove joint. There was even a particular sort of nail that might be used for becoming a member of edges. Extra fashionable strategies of reinforcement embrace dowels, biscuits, Festool Dominos and pocket screws.
Nonetheless, we contend that if in case you have two surfaces that can mate completely then you definitely don’t want further reinforcement. A well-made glue joint is stronger than the wooden surrounding it.
One other space of confusion: Different early accounts advocate utilizing a “spring joint” when gluing up a panel. A spring joint is when the sting joint has a small hole (only some thousandths of an inch) in the course of the seam. Once you clamp throughout the center of the panel, it closes your entire seam.
The benefit of a spring joint is that you simply use fewer clamps to make your panels. Additionally, in case your inventory is somewhat moist, a spring joint can hold the ends tightly collectively because the inventory dries out (finish grain loses moisture far more quickly than face grain).
Some opponents of spring joints say that the hole introduces some stress into the panel that would (in time) trigger the joint to open. Different opponents say that spring joints are merely a waste of excellent store time.
In our store, the opinion is split.
Writer Steve Shanesy and Senior Editor Robert W. Lang don’t use spring joints. And so we’re going to point out Lang’s method, which makes use of a powered jointer with none particular setups to introduce a spring joint.
Senior Editor Glen D. Huey likes spring joints as a method to scale back the variety of clamps he wants to make use of. He found out a reasonably easy jointer setup and hand trick that makes spring joints a straightforward factor to do on the powered jointer.
After which there’s me. I like spring joints and I like making them utilizing handplanes. And so I’m going to point out you learn how to make an edge joint utilizing historic strategies I’ve dug up from the previous books.
So step away out of your desk noticed for a second and try these three time-tested strategies and determine which one can be finest for you.
— Christopher Schwarz
Jointer – No Spring Joint

1. Finest face ahead. These three items got here from the identical board, and I mill them about 1⁄16″ thicker than I want. I additionally rip the boards wider – total the three are about 1″ too huge and three″ or 4″ too lengthy. After I’m pleased with the association visually, I mark a part of a triangle on the faces with a lumber crayon.
My method to edge becoming a member of comes from my coaching in manufacturing outlets, and my philosophy {that a} joint underneath stress will increase the possibilities of failure sooner or later. I don’t use a spring joint, and I run edges over a well-tuned jointer simply earlier than gluing. There isn’t something romantic or inspiring about my method, however it works effectively, and it doesn’t take lengthy.
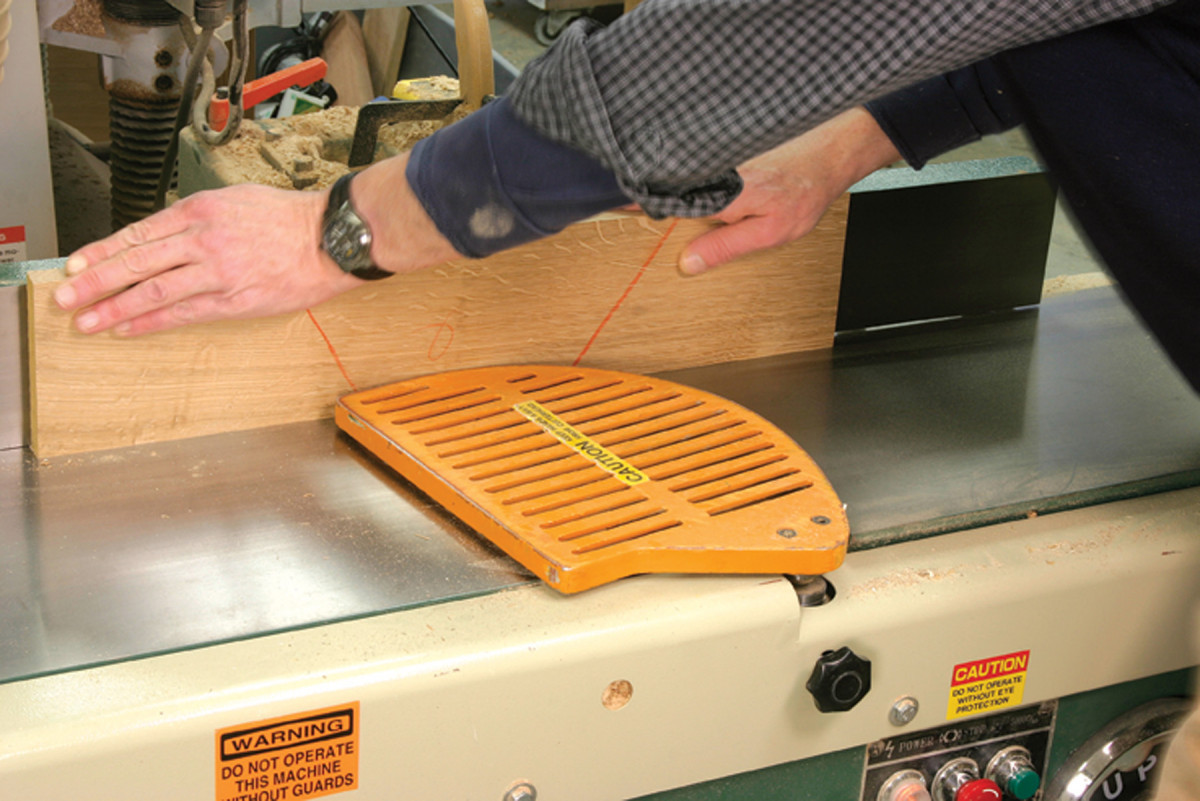
2. One in, two out. I run every edge to be glued over the jointer, alternating the faces to compensate for any small error within the jointer fence. Conserving monitor is straightforward. On the primary edge the marked face goes towards the fence. On the subsequent piece, the marked face goes out on each edges and on the final piece the marked face goes in.
I’m a bit persnickety about machine set-ups, and I get cranky if I’ve to recollect what space of a machine is off somewhat, and in what course that offset is. In fact, I’ve hassle remembering issues like that, so it’s simpler to have the jointer knives even with the outfeed desk and the fence sq..
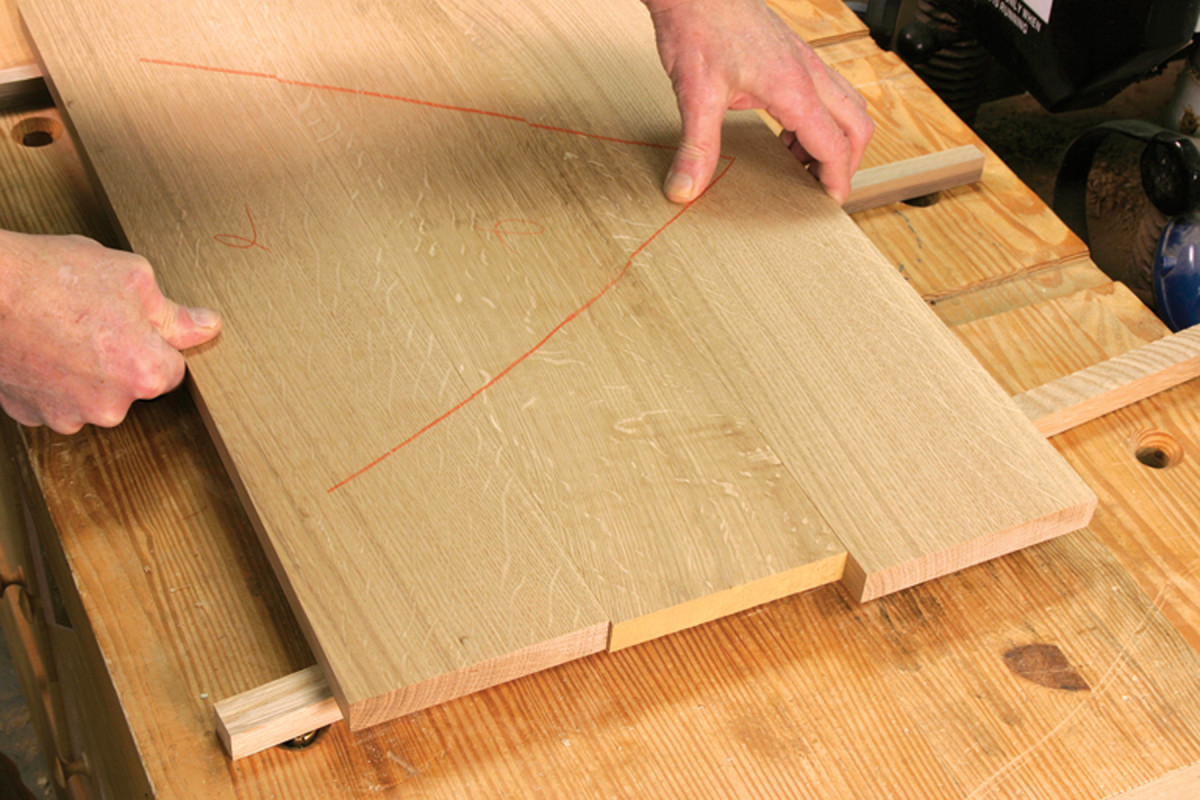
3. Examine earlier than gluing. I place the boards throughout small strips of wooden to make it simpler to align the faces, and to maintain glue off the benchtop. I be sure that these items are straight and precisely the identical measurement. If the bench is flat, the help strips equal in thickness and the sides of the elements true, I can squeeze the elements collectively by hand and never see any gaps.
I choose wooden for panels and tabletops primarily based on look. You may’t persuade me that there’s a bonus to alternating development rings, or arranging the boards so they are going to be simple to airplane in a while. The objective is to make a pieced-together board seem like it grew that approach. If the fabric is ready accurately I don’t fear about it warping, and if I have to fuss somewhat when doing the ultimate smoothing, that’s OK.
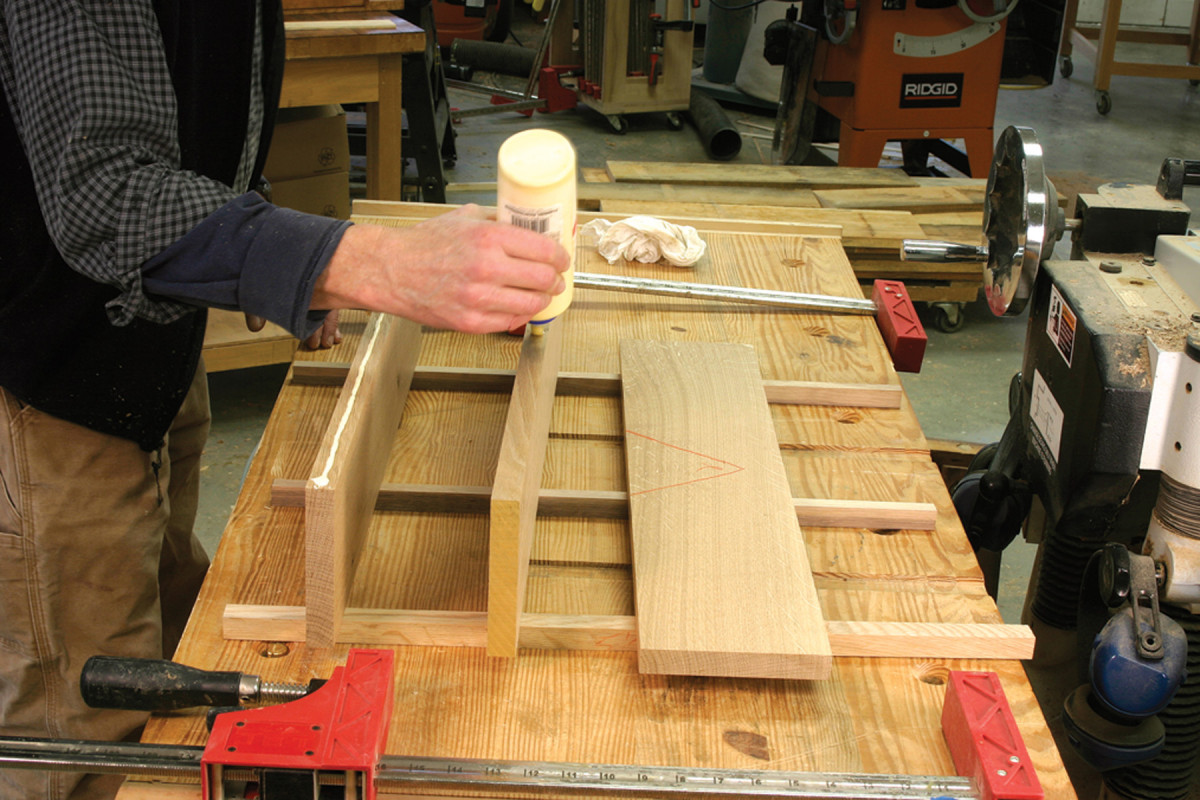
4. Edges up. I flip the primary two items up on edge and apply a single bead of glue. I don’t want to use glue to each items or unfold it round. That occurs mechanically when the elements are clamped collectively.
That is an space the place mastery of the basics is the important thing to success. Lifeless-flat boards with straight and sq. edges are simple to place collectively.
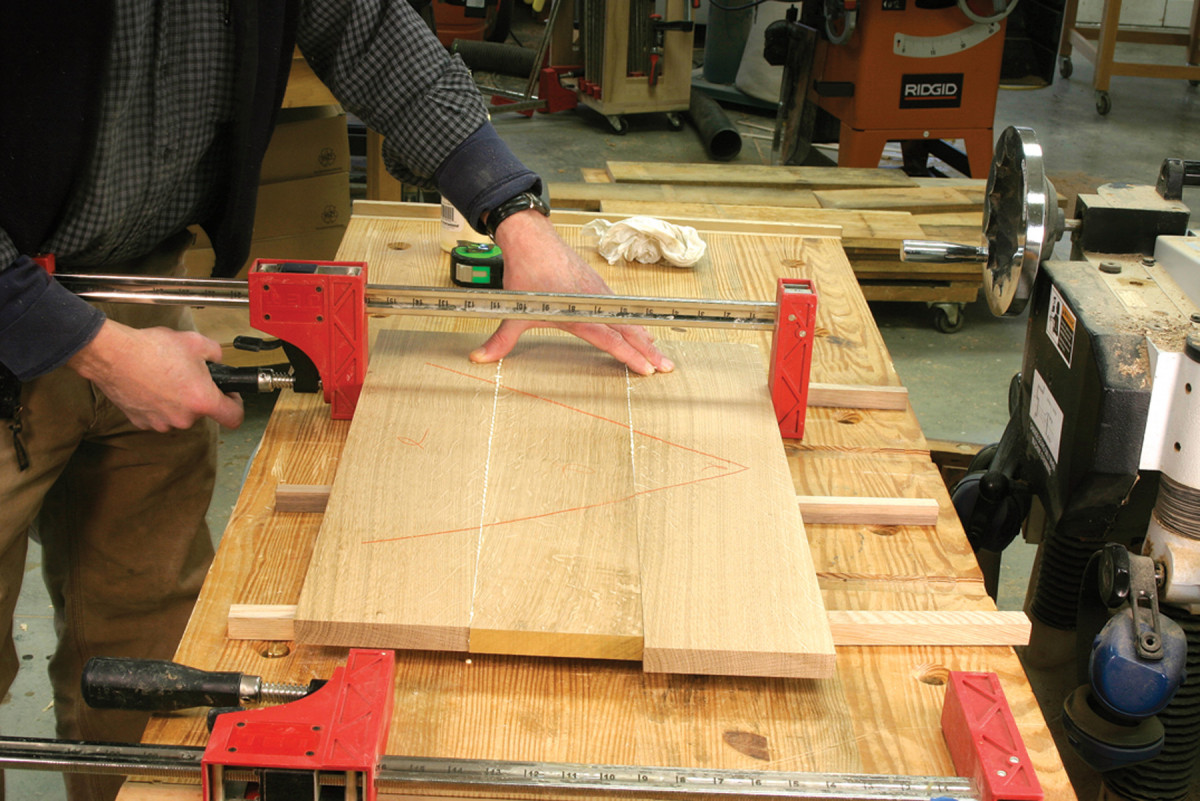
5. No wrestling. It doesn’t take a lot strain to clamp the boards collectively. My left hand holds the boards down on the help strips to maintain the faces in line. A small quantity of strain from the clamp will shut the joint for a lot of the size – if the sides are straight.
Glue them collectively on a flat floor and it could possibly truly be an pleasing, stress-free expertise. If the boards are straight and the thickness constant earlier than gluing, there’s little to be finished afterwards.
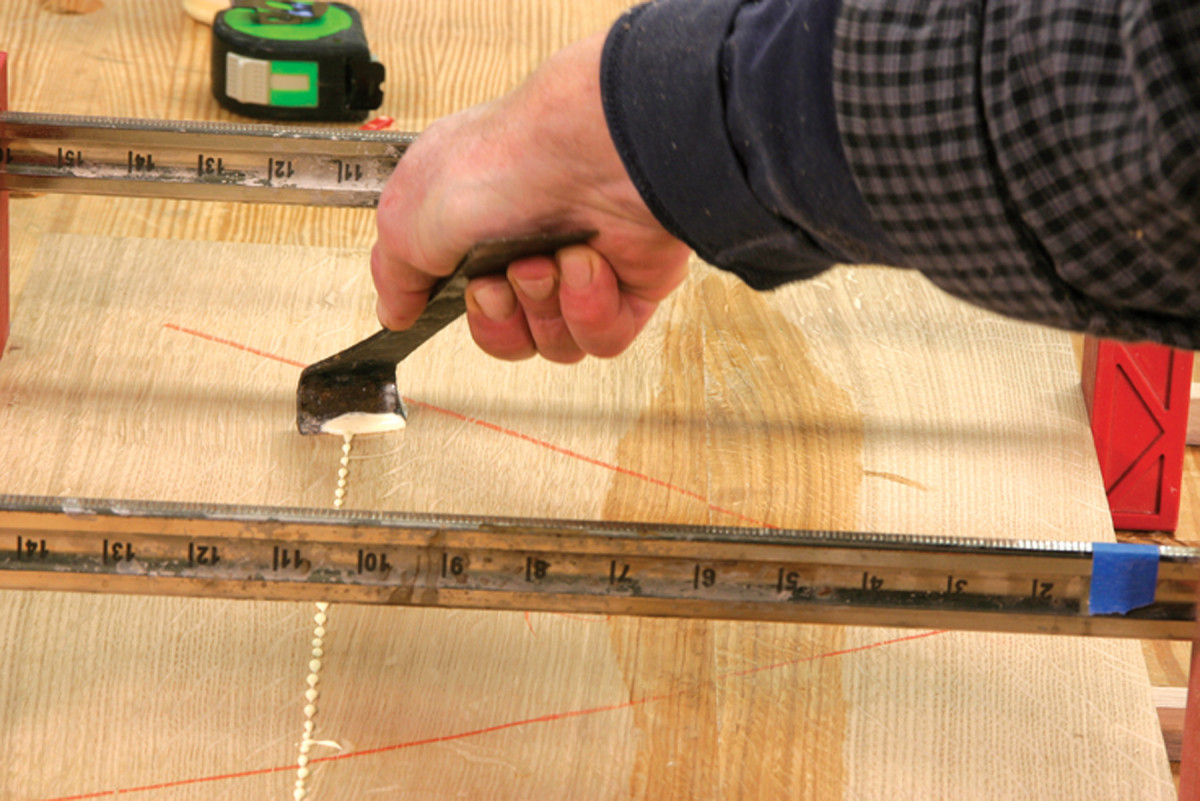
6. Clear up instantly. I scrape off the surplus glue, then wipe with a humid rag. If the glue bead dries on the floor, it slows down the drying course of, and traps moisture from the glue within the joint. I believe it makes a weaker joint.
I crosscut the tough lumber to concerning the measurement I want, however once I floor, edge and rip I’m considering WAP and TAP – “huge as potential” and “thick as potential.” This leaves some margin for me to work round defects or ugly spots with out beginning over. I attempt to hold elements from a single board collectively to make it simpler to match shade and determine.
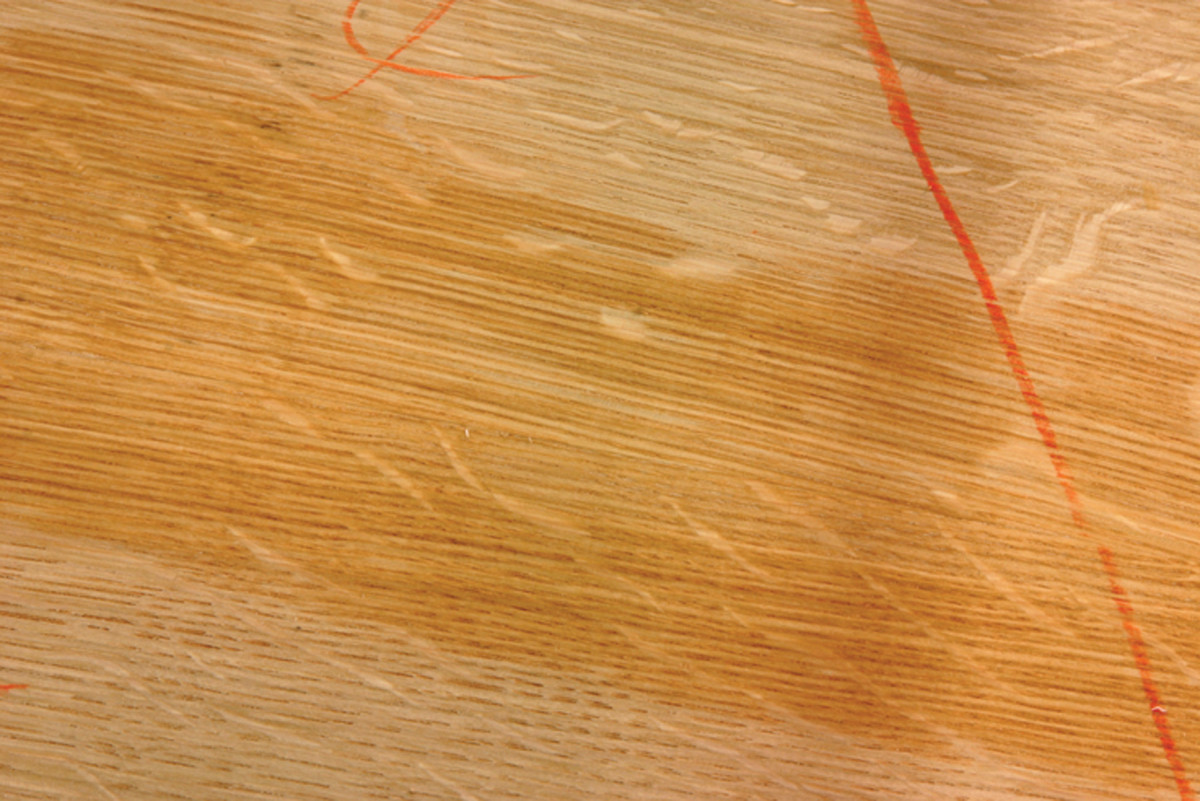
7. Good to go. The completed glue line is almost invisible. After letting the glue dry for an hour, the clamps could be eliminated. Full curing takes longer, so I let the meeting dry in a single day earlier than additional surfacing. If I do it proper, it solely takes a couple of swipes with a card scraper to scrub up the panel.
There might have been a time when a spring joint made sense, particularly if the moisture content material of the wooden was too excessive. At the moment, it makes as a lot sense as collar stays and celluloid dickies. — Robert W Lang
Jointer – With Spring Joint
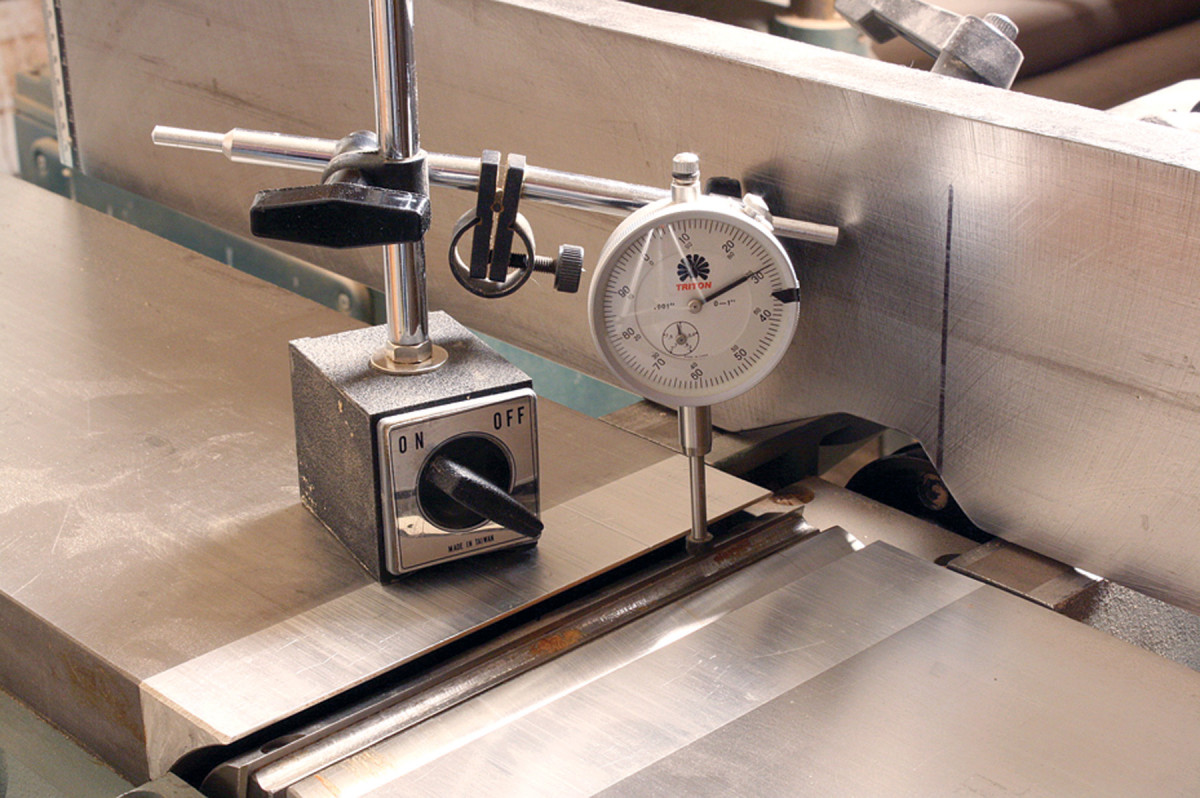
1. Bust the parable. Even when your jointer knives are set out of parallel to the outfeed desk, sloped .030″ over the 8″ knife and set .015″under the outfeed desk on the tip closest to the operator, you’ll nonetheless acquire a flat floor on the face of your inventory as a result of the knives are a straight edge. On a typical 3⁄4″ edge, the variation back and forth is a negligible .003”.
I put together my edges with a jointer, however I additionally like a small spring in my joint. As a result of I’m not a handplane aficionado, I flip to a machine. In consequence, I’ve to bend the foundations.
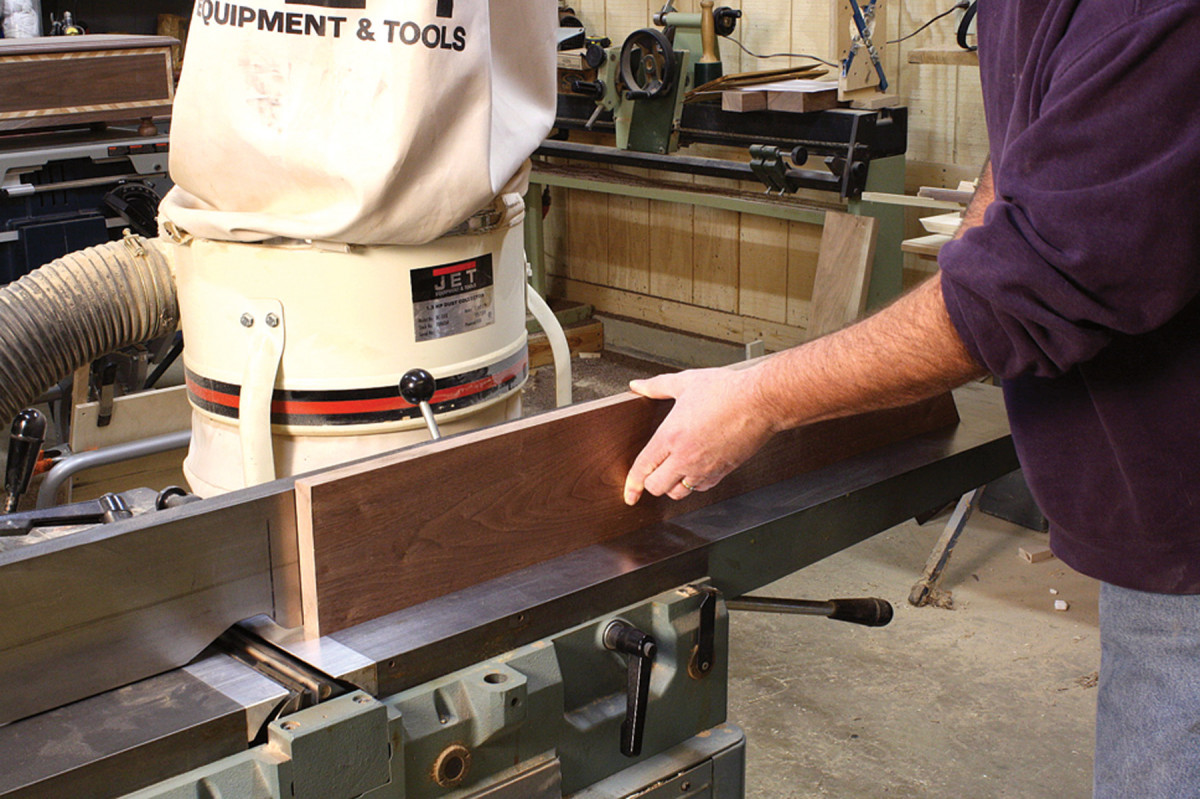
2. Hand placement is crucial. After the knives are adjusted, in case you switch your arms to the outfeed desk as a minimize is made, you’ll get a tapering minimize on the sting. With this setup you could place your hold-down hand on the middle of the board. Because the minimize is made the board rides up the upper outfeed desk till your center-placed hand transfers the strain to the outfeed facet. At all times place your strain on the middle of the board. Be aware: The guard has been eliminated for readability.
In most articles on setting jointer knives you’re instructed to make use of a dial indicator to set the knives completely stage and in line to the outfeed desk. That’s bunk.
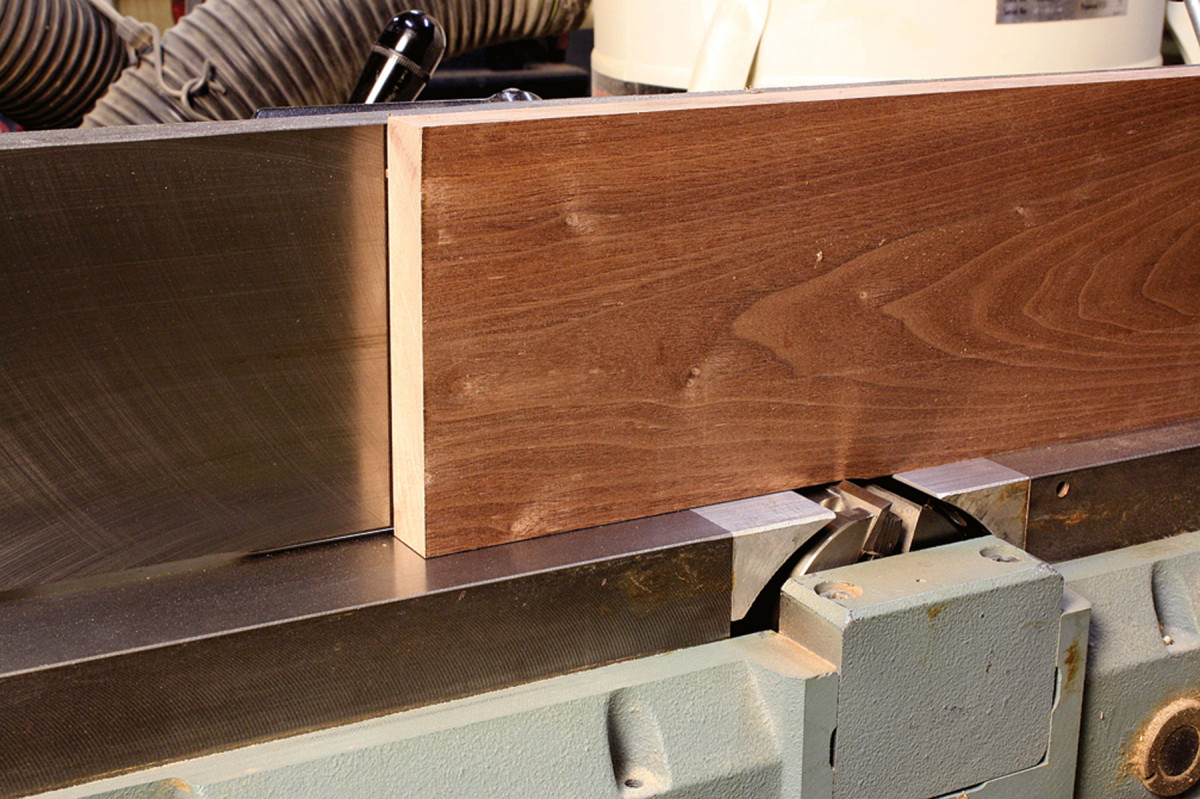
3. Up, up and away. Right here you’ll be able to see how the piece rides off the outfeed desk because the minimize progresses. If the ensuing spring is simply too giant, merely slide the fence again to lower it. (Your fence place will fluctuate with the board’s size.) After a pair passes you’ll discover the candy spot the place the minimize delivers the suitable bow for a correctly sprung joint.
When you do have to set the knives stage to at least one one other, alignment with the outfeed desk is non-obligatory. I set my knives so there’s .030″ of slope over the 8″ blade. The tip of the knives closest to the operator are under the outfeed desk by .015″. On the again they’re .015″ above the outfeed desk.
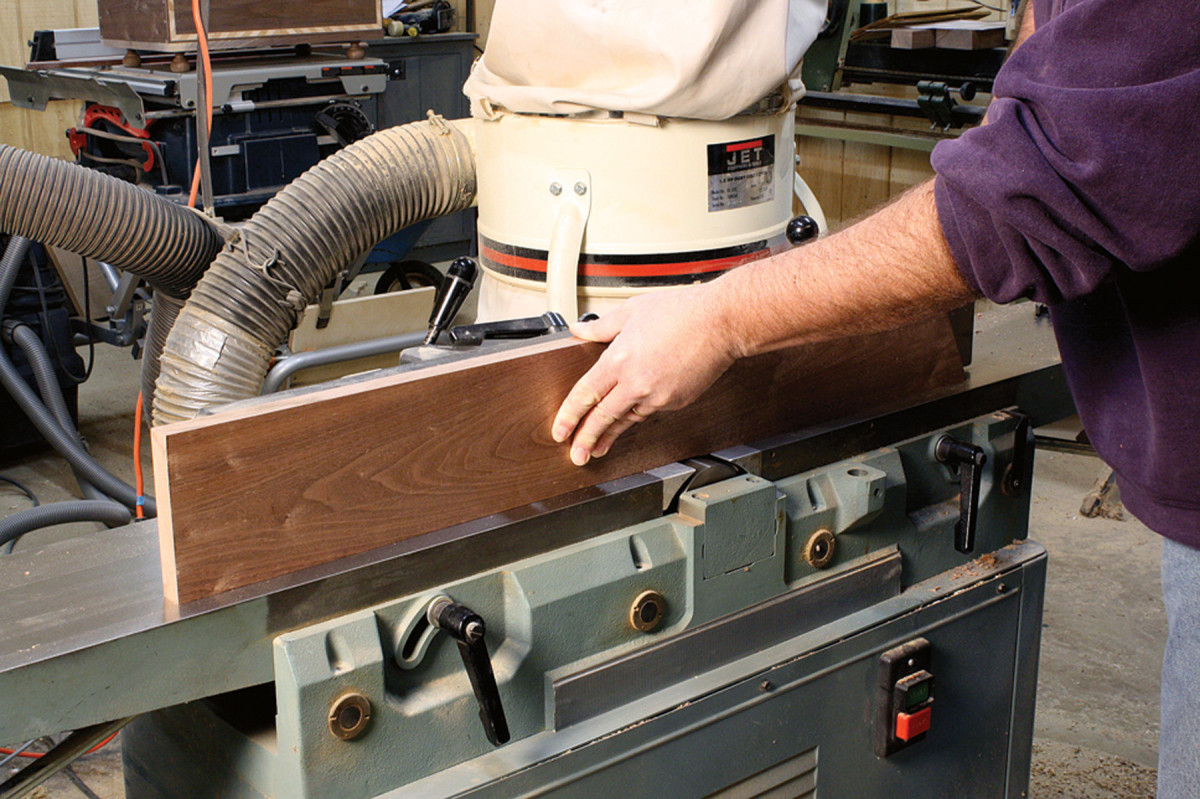
4. It occurs mechanically. As you progress via the minimize together with your strain positioned on the board’s middle, the switch onto the outfeed desk will occur in the course of your cross. The switch is gradual, so don’t count on a fast “slap” as the tip returns to the desk. With the switch of downward strain onto the outfeed desk full, a slight taper is created over the remaining size of the workpiece.
With the knives under the outfeed desk, you’ll get a taper in case you switch hand strain to the outfeed desk as quickly as there’s ample floor to take action. That’s one other rule I select to not comply with given my blade association!
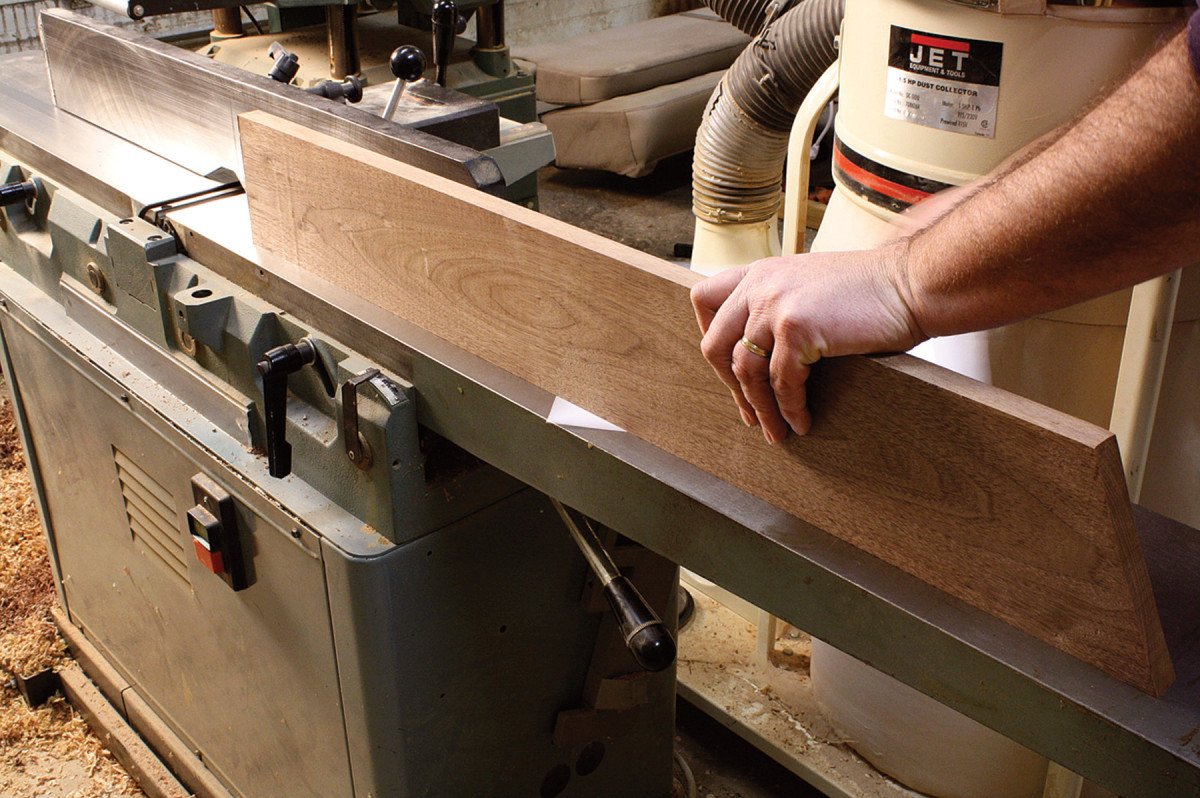
5. Hold it skinny. The concept is to create a bow or spring within the board that enables the ends of the joint to be tight as the middle hole is closed underneath clamp strain. Should you create a spot that’s too giant, the strain on the middle of the board may turn out to be overly sturdy and trigger stress on the glue line. And also you don’t acquire something if the bow is simply too gentle. I discover a candy spot the place a single sheet of paper slides whereas each ends are in touch with the jointer mattress. One other check is to position not more than a enjoying card between two board edges as you dry-fit the panel.
When edge jointing, I hold my downward-pressure hand on the middle of the board. Because the board runs over the knives it climbs barely above the outfeed desk. On the middle of the board my strain transfers to the outfeed desk and the slight tapering impact completes the minimize. Bingo, a spring joint.
And don’t fear about flatness when face jointing. As a result of a jointed face just isn’t the ultimate floor when milling for thickness, any small variations are erased at a planer. And in case you’re nervous concerning the small bevel on the sting of a 3⁄4” board, you’re lower than a .003″ variation.
Backside line: I can dial in my spring joint by adjusting my fence place alongside the blades. When all the pieces works as deliberate, I want just one clamp for many panel assemblies, however I usually use two. — Glen Huey
Handplanes
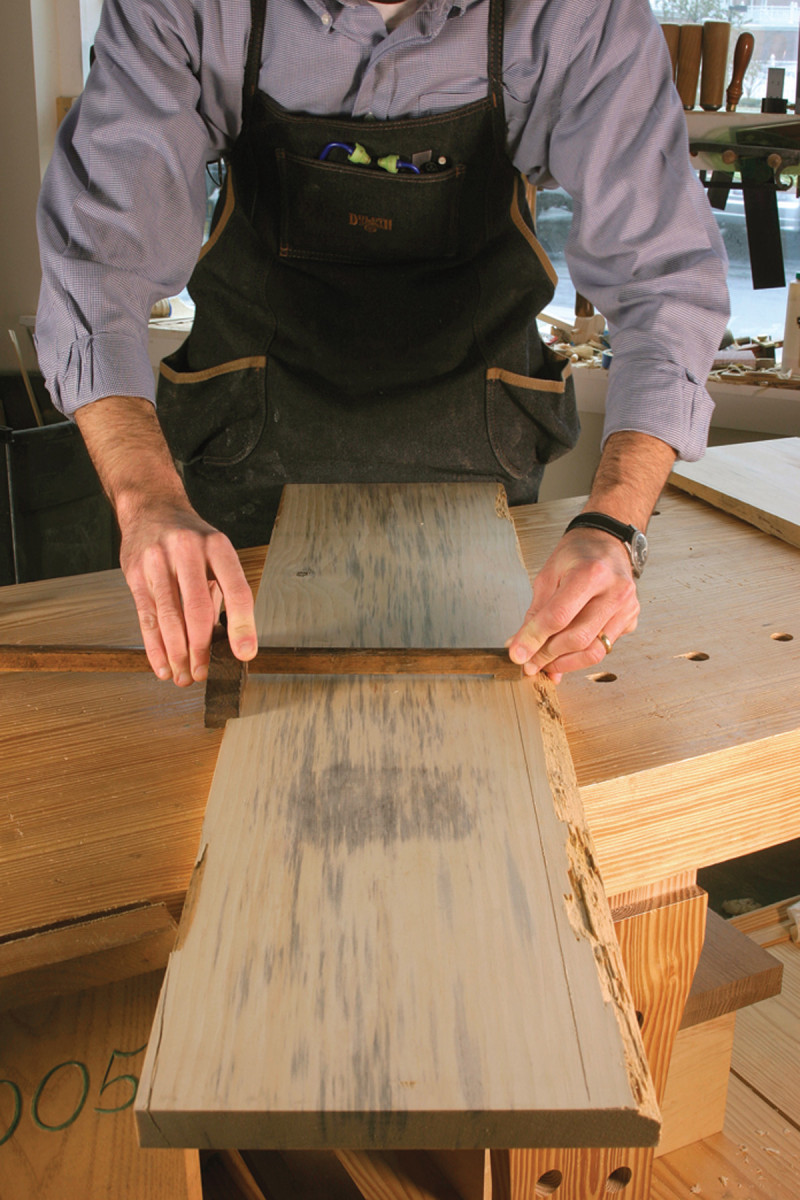
1. Gauge your width. I take advantage of a panel gauge to scribe the ultimate width on my boards. Scribe the width on each faces of the board.
Though I first discovered to organize edge joints by machine on a powered jointer, I favor to do it by hand at any time when potential. After I’m working for myself and time isn’t a priority, I’ll use the pure hand-tool strategies proven right here. It’s a bit slower than the power-tool strategies, however I take pleasure in it immensely.
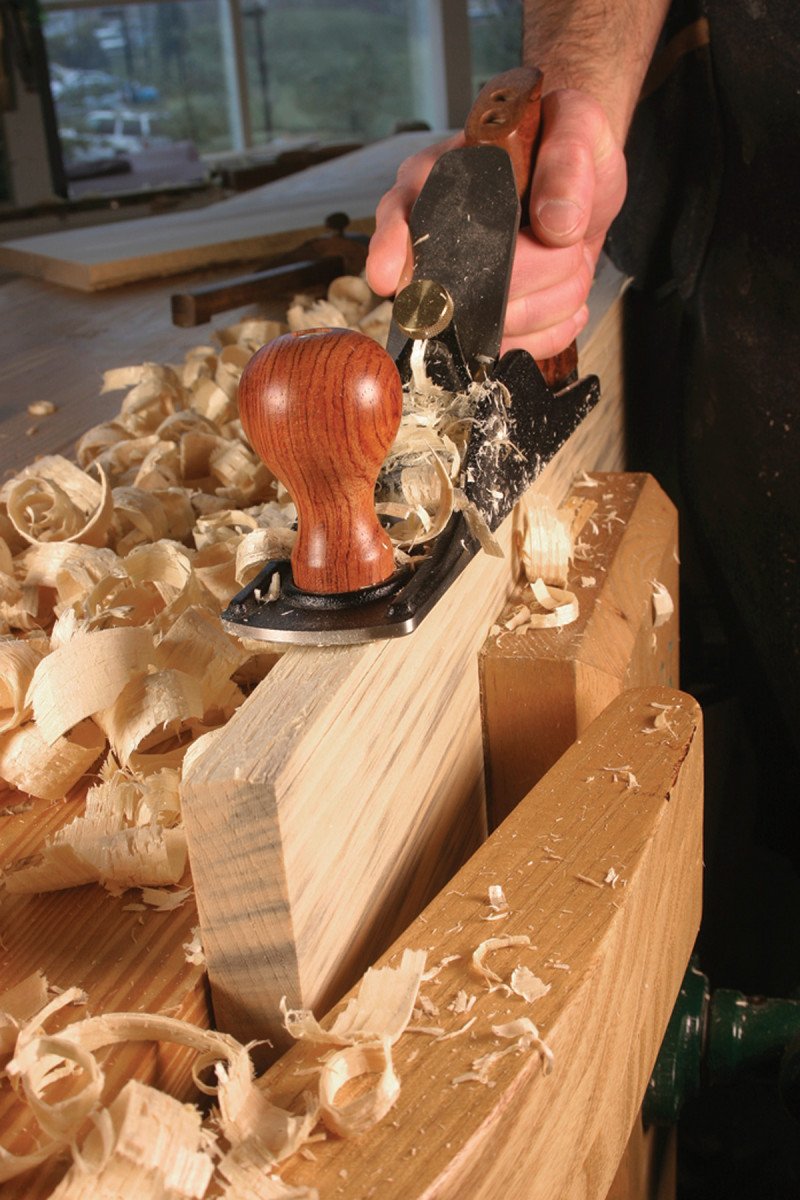
2. Rip with a airplane. I take advantage of a scrub airplane to work right down to the road left by the panel gauge. Use brief uneven strokes and every cross can take away 1/16″. I diminished this board by 1″ in width throughout one pop track on the radio.
When each second counts, nevertheless, I’ll put together my edges on an influence jointer after which use a jointer airplane to introduce the spring joint. You may combine and match the hand and energy strategies any approach you see match.

3. Joint and examine. Costume your edge with a jointer airplane, then use a sq. to substantiate that your edge is true to at least one face of the board.
Listed here are a pair particulars and subtleties of my course of. Although I take advantage of a scrub airplane to decorate my tough edges, you may as well use a desk noticed, band noticed, drawknife or a hatchet for the coarse removing of fabric.
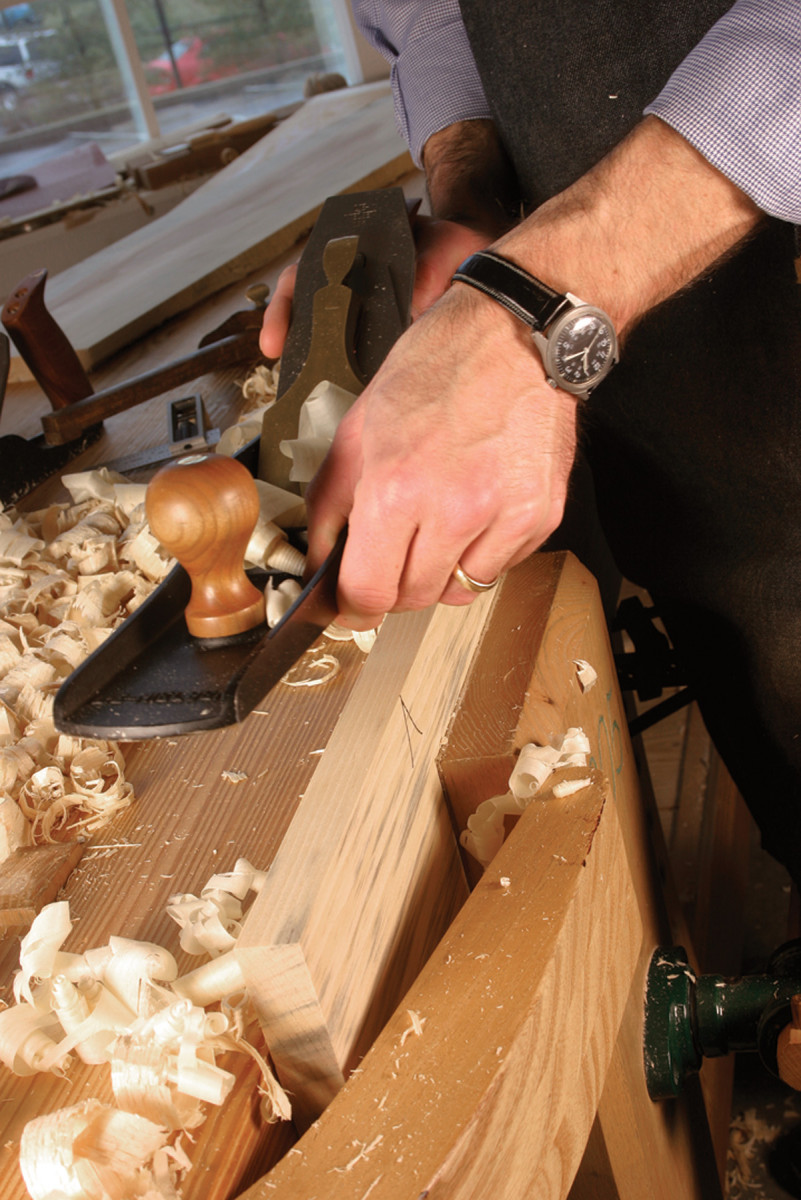
4. Spring the middle. Right here’s the enjoyable half. Joint the sting, however start the cross about 5″ in from the tip of the board and raise the airplane off about 5″ from the opposite finish of the board. That is known as a “cease shaving” as a result of it doesn’t run your entire size of the board. One cross (or two) needs to be all you want, relying on how deep your cutter is about.
Additionally, the cutter in my jointer airplane has a really refined curve on its edge. This permits me to appropriate an out-of-square edge by shifting the airplane left or proper on the sting of the board.
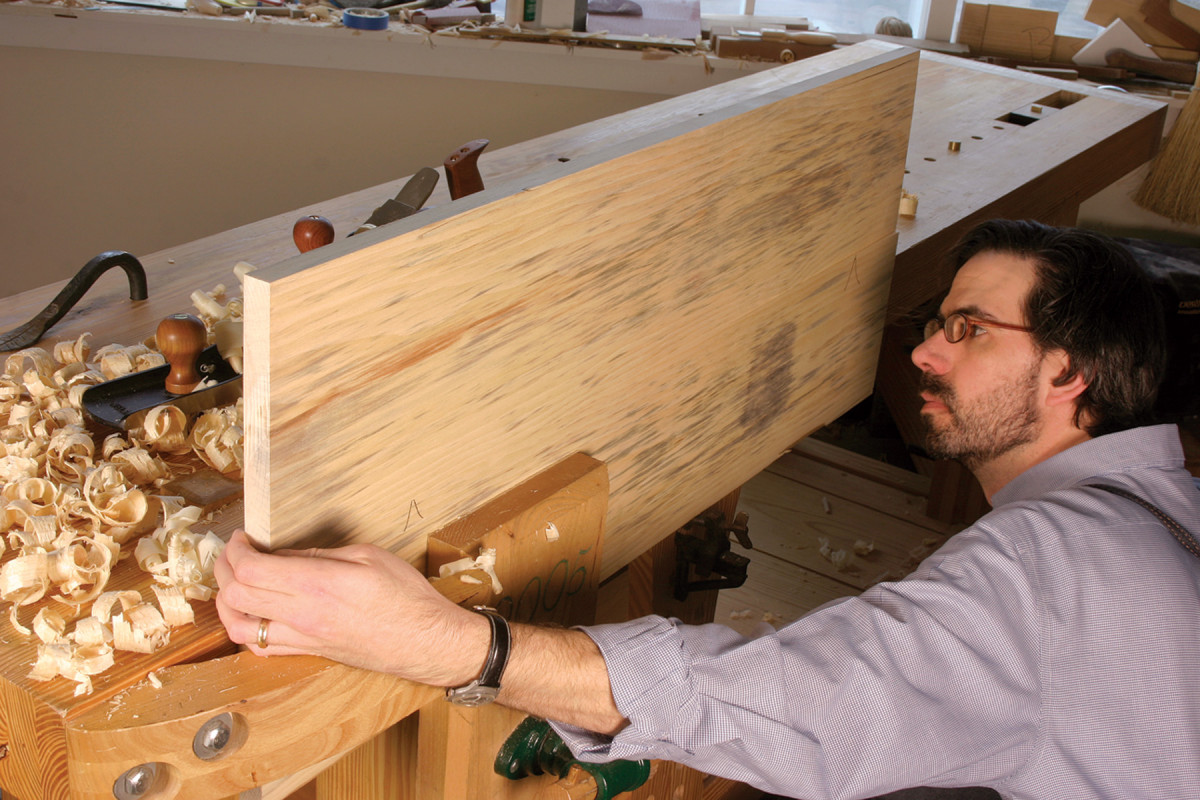
5. Do they mate? With one edge spring jointed, put the board’s mate on high of the primary board. Wiggle the highest board on the finish. Should you can really feel drag on the ends you’ve a spring joint. If the highest board pivots simply on the middle you’ve a hump in the course of one (or each) edges and you could attempt once more.
However the curve just isn’t so pronounced that it produces a curved edge on the board. The sting appears to be like flat to a attempt sq..
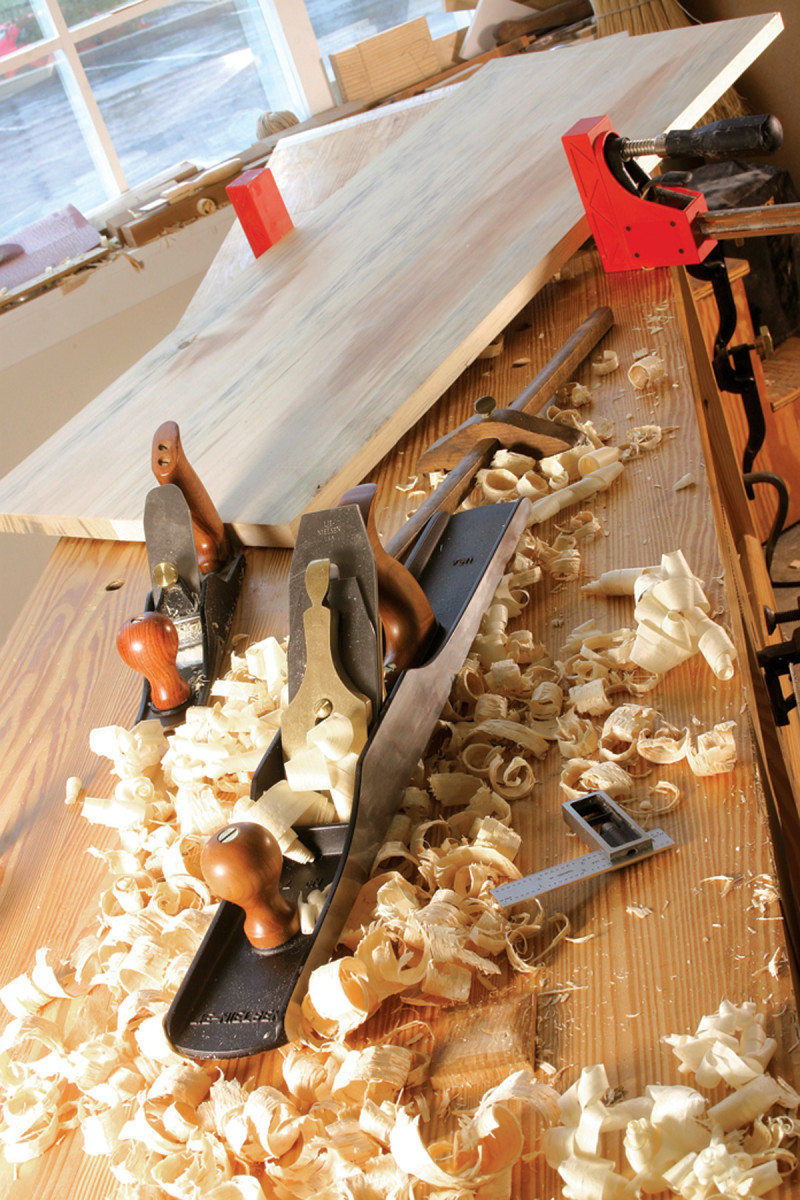
6. Outcomes. With small panels (as much as about 36″ lengthy) I can get away with utilizing one clamp within the middle. Bigger panels would require clamps on the ends of the panel as effectively. pw
You may learn extra about this course of within the August 2005 challenge (#149) of Common Woodworking in a wonderful article by David Charlesworth titled “Studying Curves.” — Christopher Schwarz
Product Suggestions
Listed here are some provides and instruments we discover important in our on a regular basis work across the store. We might obtain a fee from gross sales referred by our hyperlinks; nevertheless, we’ve fastidiously chosen these merchandise for his or her usefulness and high quality.